Calders & Grandidge uses cookies to deliver superior functionality and to enhance your experience of our websites. Information about our cookie policy can be found here.
Continued use of this site indicates that you accept this policy.
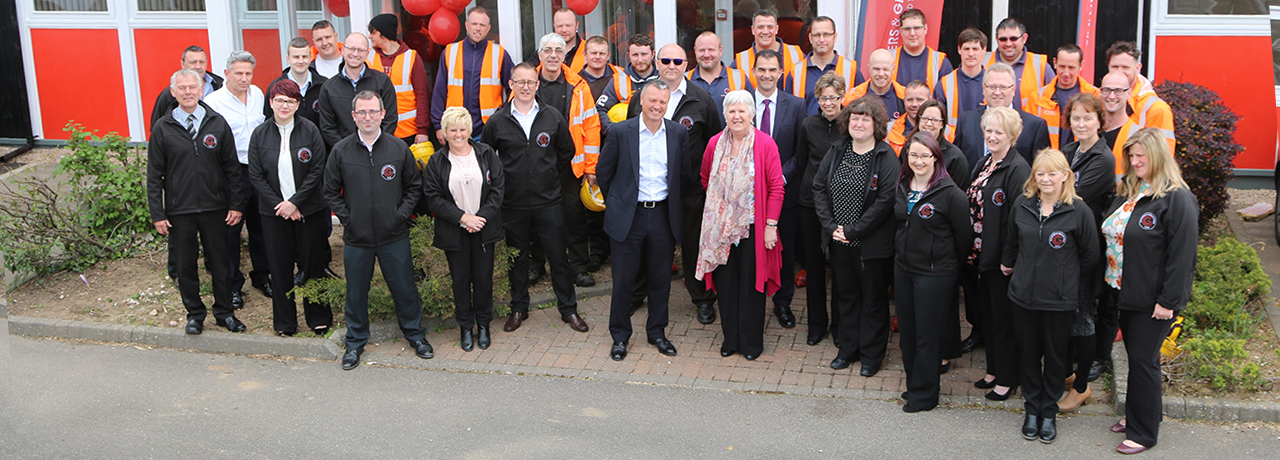
Meet the management team
Committed to excellence

Andy joined the Saint Gobain Group in 1996 as Branch Manager of Jewson progressing into several roles across the business. He was then appointed to the role of Managing Director of Calders & Grandidge in 2020.
As Managing Director he is responsible for the overall strategy and performance of the business and this starts with Health & Safety, which is always a priority. After this Andy’s main areas of focus are employees and customer satisfaction. Calders & Grandidge has a long history in the timber supply and treatment market.
Andy’s vision is to ensure the continued growth of the business by focussing on customers now and into the future.
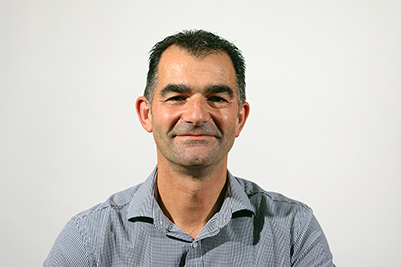
John is the Business Director for the site in Boston and has overall responsibility for the general and strategic management of our activities and the performance of the business.
John’s passion to work within the timber industry started when he was 16 years old and he is proud to work for the market leaders in timber preservation with a great team of experienced knowledgeable colleagues.
John also sits on the board of the Wood Protection Association who are dedicated to improving the performance and value of wood as a sustainable construction material.
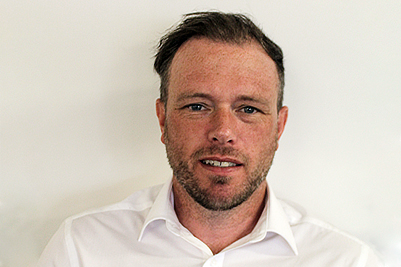
The primary purpose of Matt's role is to manage, champion and promote Health, Safety, staff well-being and Environmental excellence by organising, monitoring, advising and training employees at all levels. In addition to responsibility for the maintenance of the EHS management system, a significant focus of the role is to lead improvement in all aspects of EHS performance. This includes leading major EHS capital investment projects. A key member of the senior management team, Matt manages all company sustainability issues and leads the setting, monitoring and presenting KPI’s that align with the EHS strategy for Calders and Grandidge.
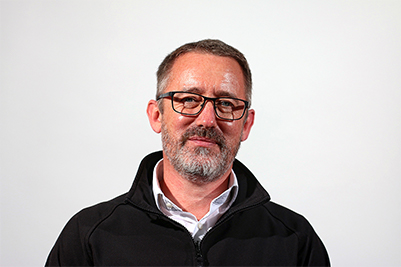
Rob joined Calders & Grandidge in 1994 and has enjoyed several varied positions throughout his career before starting his current role as Commercial & Technical Manager in 2019.
With a firm background in manufacturing, product quality and procurement, as well as being a key member of the senior management team for Calders and Grandidge, Rob’s responsibilities include; timber procurement for all areas of the business, stock control, day to day contract management, sales to new and existing customers in the Pole and Track markets as well as providing technical support to all areas of the business.
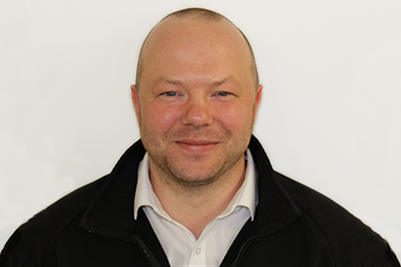
Darrel joined Calders and Grandidge as an apprentice and has worked his way through the ranks to be the position of Production Manager.
His primary focus is to ensure continual growth of the business, whilst maintaining the core values of the company. He is responsible for a team of 40 men and has control of all KPI’s relating to all production activity on site.